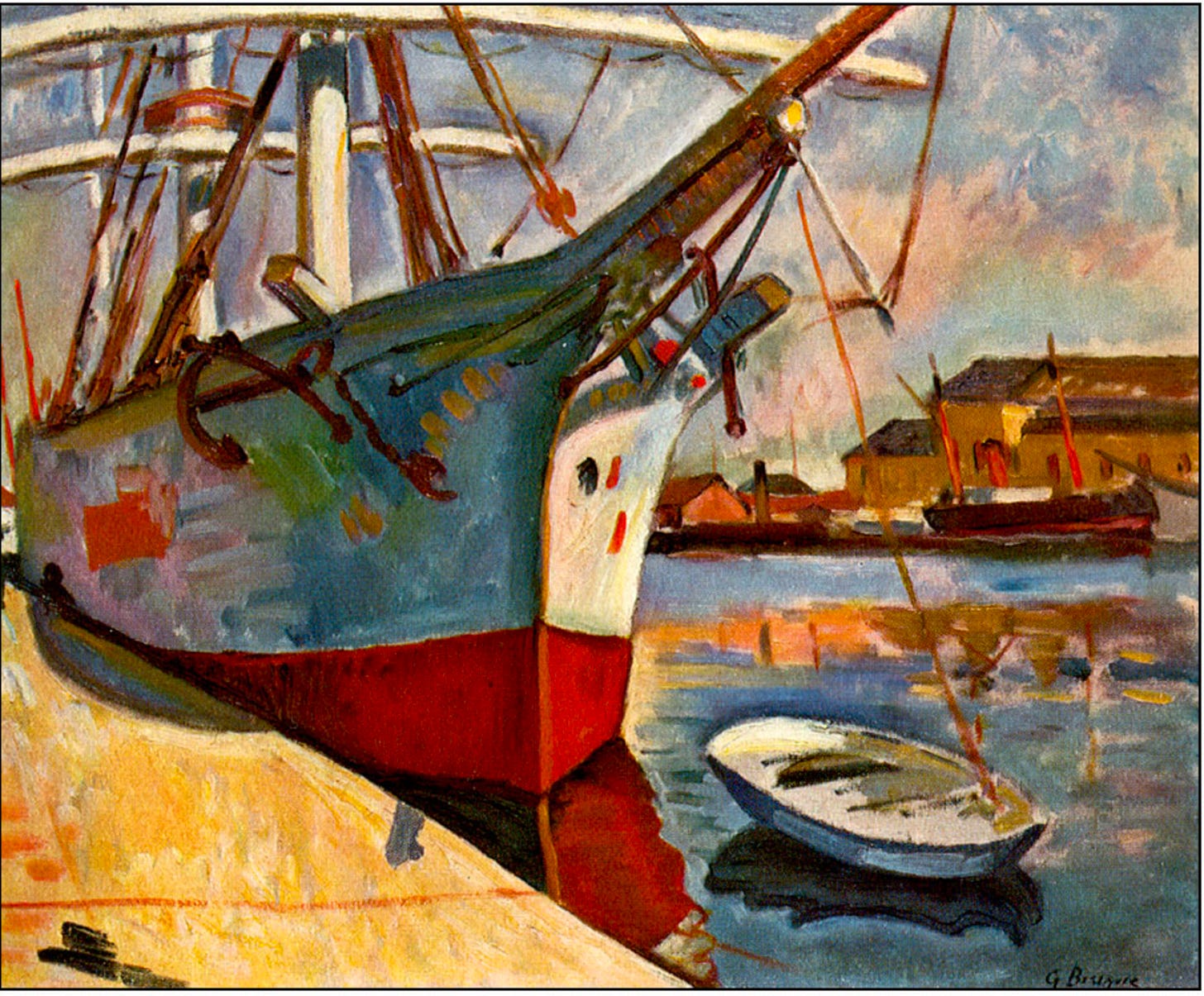
Art: Georges Braques, Ships at Le Havre, 1905
Last week, a woman posted in my local Nextdoor group, asking people to please, please donate PPE - personal protective equipment like face masks - to doctors and nurses at our neighborhood hospital.
Face masks are in perilously short supply right now around the world, and particularly in America, where, because of the surge of potential coronavirus patients in hospitals, medical professionals are now having to reuse them, or in some cases, go completely without.
There are many reasons why we currently don’t have enough masks, including the American government ignoring warnings to prepare for coronavirus, and people panic-buying heavy-duty masks.
Where does all our stuff come from?
But the key reason is probably the fact that America has outsourced much of its mask production overseas, and the supply chain for producing these masks has become so complicated that no one person knows all the steps of the process.
The seeds of that problem, says Bowen, can be traced back 15 years. That's when many mask factories moved overseas, where masks could be made at a fraction of Bowen's costs.
Most notably, he says, Kimberly-Clark, which used to be one of the industry leaders, moved its operations.
"The surgical mask supply went from being 90% U.S.-made to being 95% foreign-made in literally one year," Bowen says.
This phenomenon in economics is best illustrated by a 1958 essay, “I, Pencil.”, which is a beautiful meditation on all the different parts that need to come together to make a single pencil.
Simple? Yet, not a single person on the face of this earth knows how to make me. This sounds fantastic, doesn’t it? Especially when it is realized that there are about one and one-half billion of my kind produced in the U.S. each year.
…..
My family tree begins with what in fact is a tree, a cedar of straight grain that grows in Northern California and Oregon. Now contemplate all the saws and trucks and rope and the countless other gear used in harvesting and carting the cedar logs to the railroad siding. Think of all the persons and the numberless skills that went into their fabrication: the mining of ore, the making of steel and its refinement into saws, axes, motors; the growing of hemp and bringing it through all the stages to heavy and strong rope; the logging camps with their beds and mess halls, the cookery and the raising of all the foods. Why, untold thousands of persons had a hand in every cup of coffee the loggers drank!
A similar description of how facial masks are made and shipped appears in a recent NPR article,
"Making masks is not as easy as you imagine. We have to make the ear loops and the metal strip, the packaging. There is a pretty big system involved," Guan Xunze, chairman of pharmaceutical group Shengjingtong in northeastern China, told NPR by phone. He's referring to the metal strip that lets you bend the mask around the nose bridge.”
Both the masks made for medical personnel and for consumer purchase require a once-obscure material called melt-blown fabric. It's an extremely fine mesh of synthetic polymer fibers that forms the critical inner filtration layer of a mask, allowing the wearer to breath while reducing the inflow of possible infectious particles.
"We're talking about fibers where one filament has a diameter of less than one micron, so we are in the nano area," said Markus Müller, the sales director at German company Reicofil, a major provider of melt-blown machine lines.
...
Timothy Robson, a business development manager at Hills, Inc. in Florida, is skeptical of the quality of such production lines, which must meet precise standards to produce the kind of masks worn by medical staff. Hills Inc. is one of the handful of companies in the world that can make the hand-drilled die tips for the machines. The melted plastic is blown out through the tips.
The Mask Problem
So you have machines that make the specific fibers made in Germany, specific parts for the machines made in Florida, and the masks themselves are made in China, and then shipped, to the United States, where they go through several levels of supply chain before reaching hospitals. On top of all of this, some outlets are suggesting that China is “hoarding” masks - a pretty incredible claim given that China is still dealing with coronavirus itself and has already ramped up production for the entire world.
Just to recap: masks require very specific machinery to make, have to be sourced from all over the world, including China, and controlling their supply is as politically charged as it is desperately medically necessary. Because of this confluence of factors, there is no one single, easy fix for getting more masks here to America, quickly.
Tech will solve the mask problem
But, where the government cannot fill the void, private individuals, many from tech have stepped in (as they tend to do). For example, Alibaba CEO Jack Ma recently sent millions of masks to Europe, the United States, and South America.

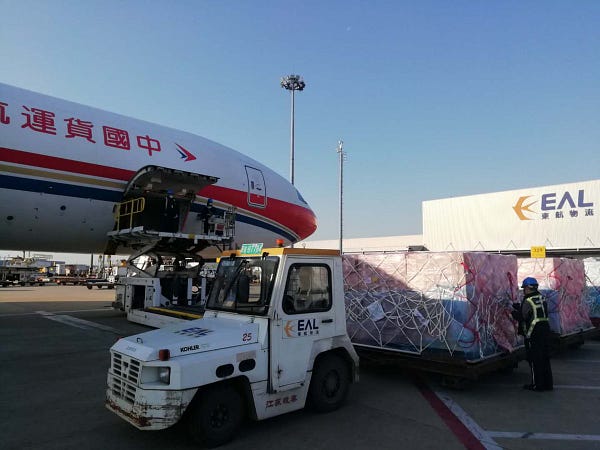
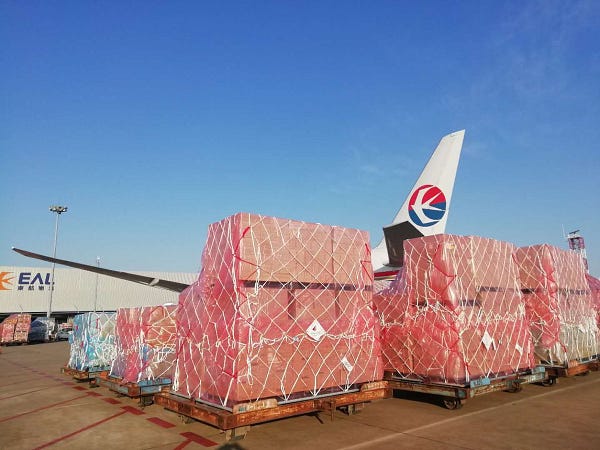
Then, there is Zuck, who was saving hundreds of thousands of face masks for employees that he’s now donating.
Apple, Tesla, and IBM have also donated. In fact, there is an entire article about why “we shouldn’t rely on Silicon Valley” for face masks and, if you have nothing else to do at home, you can read the back-and-forth between the writer of the article and commenters who scornfully ask how many masks the writer himself donated.
In probably the strangest and most interesting move, there is Paul Graham. I wrote about him in my first Normcore post, because I think it’s hard to underestimate the impact he’s had on the past fifteen years’ worth of people starting tech companies. Understanding him is an essential part of understanding the current popular cultural norms of Silicon Valley.
At the time, I wrote,
He had a fantastic way for elucidating the common realities we’re dealing with in tech and turning them from a frustrating jumble of noise into clear, elegant writing that describes exactly what people are dealing with. “I know what it’s like,” his earlier posts, which were kind of like reading letters from an older, smarter brother.
It’s hard to pinpoint exactly when the tide turned, but it’s very much tied up in his success at YCombinator. In 2009, the company moved from the East Coast to the West Coast. In 2011, Yuri Milner, a Russian-Israeli investor with investments in the top internet-based companies of the past fifteen years, got involved. Sometime between then and 2014, when Sam Altman (who once tried to change US politics with a dashboard), stepped in, Paul Graham no longer was writing from outside the establishment.
In his position as an insider, he’s again been saying doing curious things that are, again, out of touch. For example, recently, in response to the proposal to track cell phones to mitigate contagion rates, he tweeted,
He ended up redacting the tweet, but then the next thing he did was to donate a whole lot of money to a company called Flexport to bring masks to America. Or, to be more specific, to Flexport’s .org arm.

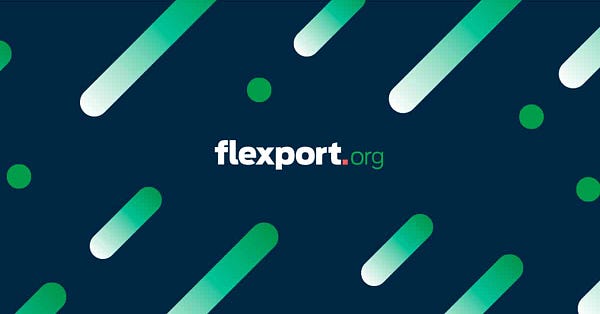
In the current situation where small groups are getting together to make more masks by any means necessary, car factories are being converted to make face masks, and even fashion designers are stepping up, you would think this would be a really positive sign in what’s proving to be the bleakest spring in my recent memory.
But, once you start looking deeper into it, things get a little more squirrely.
First, it helps to know a little about Flexport. The company describes itself as a freight forwarder, or organization that coordinates between companies that produce goods and companies that consume them. It doesn’t actually ship the goods, but it coordinates all the transportation necessary for the goods to be shipped. It also takes care of the freight clearing customs, being weighted, basically all the logistics around freight. Freight forwarding is, traditionally, a very messy and manual business, involving tons of paper and PDFs for things like bills of lading, invoices, licenses and lists. And, of course each freight forwarder handles the documents in a different way, as does each client. The space, as the VCs say, is ripe for disruption.
That’s where Flexport comes in. Flexport is a freight forwarder that bills itself as a tech platform to give companies shipping goods more visibility into the status of their freight. It is also a YCombinator company.
Flexport’s CEO, Ryan Petersen, has previous experience in the space, having started a company that exported to and imported goods from China:
In the late ‘90s I started working for my brother, importing scooters, ATVs and dirt bikes from China and selling them on the Internet in the U.S. Starting in 2005, I spent two years in China, learning Chinese and managing the supply chain. I was a customer of freight forwarders and it was entirely too difficult to ship things internationally.
He went on to organize shipping data, and then founded Flexport, looking to build out almost an end-to-end platform for all the parts of the shipping process.
It’s almost like speed dating or a meetup for freight companies. You go to China and you might meet 50 companies in three days for 45 minutes each. You learn about their capabilities and you meet their team. It’s a relationship business. Though I’ve found that when someone says, “This is a relationship business,” that’s a code word for inefficiency. I think technology can make people better at relationships. Facebook made me better at remembering birthdays.
We act almost like a Facebook for trade. For example, Warby Parker is one of our customers. We also have some of Warby Parker’s suppliers as customers. Warby Parker invited them to be part of our system, so Warby Parker can buy from those factories through our system and we deliver the goods.
Y Combinator found this idea very compelling, and invested in 2015. At that time, Paul Graham had this to say about it:
“There will be more international trade because of Flexport and international trade is a very big thing for there to be more of.”
By that point, he’d already stepped down as president of YCombinator in favor of Sam Altman taking over. And now, it’s unclear what, if any, financial interest PG has in the day-to-day investments of the incubator. It’s entirely possible that this is a completely philanthropic action for him.
But I think the truth is a little more complicated than that, and I also think it’s safe to say that he’s not partnering with Flexport purely out of the goodness of his heart. He ostensibly still has a financial interest in seeing portfolio companies do well.

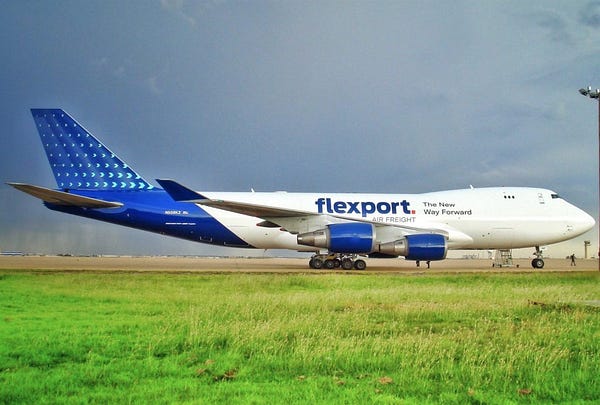
But, brushing aside my evergreen cynicism, let’s do a thought exercise. Let’s say that it makes sense for Flexport to be involved with the mask business, particularly given that Petersen has previous experience working in China and potentially a lot of good connections there.
Even given all of those advantages, what can Flexport gain here? The problem is not in itself the shipment of masks - China said it won’t even ship anymore, and Germany and South Korea are clamping down. The problem is that we in the United States need to ramp up mask production as soon as possible.
How many masks can you make with a million?
Given that it’s not the shipping but more the supply and production of masks that’s the problem right now, what can Flexport do with $1 million?
PG says, a lot,
Yes. The root of the problem is that the hospitals' supply chain is brittle, and broke under the stress. One hopes it will get redesigned to be more robust. But in the meantime Flexport can get PPE now, and now is when it's needed.
It looks like Flexport is able to deliver, based on a previous tweet from San Francisco mayor London Breed:

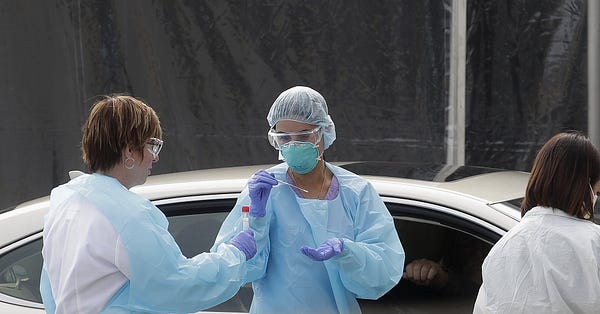
(By the way, it’s interesting that Petersen discounts human relationships in the supply chain since it seems like the only way the city got those masks is because he reached out to the city.)
But all of this is very handwavey and opaque. For example, where and how did Flexport get those masks? And, how is Flexport.org, the non-profit organization actually handling delivery, related to its parent company, and how are their financial structures related? Moreover, why does the .org even exist?
My cynical thinking, again, is that it’s a way to beta test very difficult shipping pipelines for lower costs so that these routes are primed and ready to go when more paying customers come around. (Flexport people, if you’re reading, please send me a message and prove me completely wrong.) And, if you click on the Flexport.org site, it doesn’t say exactly where and how the donations work with respect to the corporate parent.
Which, to me, means two things can be true at the same time 1) Paul Graham is extremely worried about public health. But 2) Paul Graham is also giving Flexport a stimulus of sorts.
A very-much needed one, for several reasons. First, international trade will see a huge downturn, as it usually does during down economic cycles, which does not bode well for Flexport’s business, unless it happens to, say, do a miraculous job importing face masks. Second, Flexport is already on shaky ground, and has been laying people off in February as a result of a lack of funding coming from SoftBank, whose fund is falling apart as we speak as a result of WeWork’s implosion. Third, SoftBank runs on Saudi and Saudi oil isn’t doing too hot right now, which is buffeting the funding environment even more. All of these factors coming together are really going to test solid businesses, much less startups tied inextricably to the global economy, over the coming year.
This was a very sad Normcore to write, because America is in a really tough position right now. We all will soon, if we don’t already, know someone who’s been impacted by coronavirus, either physically, or economically.
It’s really hard to be cynical about deliveries of masks that our medical professionals, who are dealing with hell every day now, need.
Nevertheless, I’ve seen too much writing this newsletter to assume that companies and individuals with large financial interests always act with one single intention in mind. Wherever there is chaos, there is opportunity, and Silicon Valley sure loves both.
What I’m reading lately:
Speaking of facemasks, how about a neural net that detects you whether you’re wearing a mask or not?
“Business knowledge should be part of a technical career path.”
More on mask procurement:
If you work at a hospital with a 24 hour emergency room in need of these items, please ask the office in charge of procurement at your hospital to visit this URL hf.tools/ppe-request so they can provide us with the information we’ll need to determine if we can make a donation.A year without conferences
Ask Reddit: When did COVID get real for you?
The Newsletter:
This newsletter’s M.O. is takes on tech news that are rooted in humanism, nuance, context, rationality, and a little fun. It goes out once a week to free subscribers, and once more to paid subscribers. If you like it, forward it to friends and tell them to subscribe!
The Author:
I’m a data scientist. Most of my free time is spent wrangling a preschooler and a baby, reading, and writing bad tweets. Find out more here or follow me on Twitter.
paul later clarified that he was baffled that people attempting to get around this system would knowingly leave their homes with their phones when they were aware it was being used to track them. this was a misleading swipe.
https://twitter.com/paulg/status/1241701618355142658?s=21
you also recently referred to Apple’s “newfound” advocacy for privacy. this message is over 10 years old and therefore that adjective is false by any reasonable interpretation of the semantics of “newfound”
https://youtu.be/39iKLwlUqBo
hai!
- atec